The quality of raw materials entering the factory has a direct impact on the quality of the finished products, making effective supplier quality critical for manufacturing success. Being a part of the larger picture of Total Quality Management (TQM), which encompasses adherence to specs, design quality, process quality, and delivery quality, supplier quality is where it all begins. However, due to shortages, logistical disruptions, and rising costs, maintaining material quality has become increasingly difficult.
According to Aberdeen’s research, the rising cost of raw materials is the top operational challenge manufacturers face in 2023, along with the complexity of global supplier networks. In this article, we’ll look at how Best-in-Class manufacturers manage supply chain quality and present strategies for prioritizing supplier relationships and planning effectively amidst disruptions.
Operational Challenges Affecting Quality Management Processes in 2023
Aberdeen’s research reveals the top operational challenges manufacturers face with their quality management processes:
- Rising cost of raw materials – 36%
- Increasing product complexity – 30%
- Complexity of global supplier networks – 25%
- Lack of training for quality assurance – 23%
- Frequent design changes – 23%
Inflation, employee turnover, and energy costs are the main culprits of the rising cost of raw materials. With fewer workers to generate and transport materials and increased cost of doing business, operating costs for suppliers are through the roof, causing suppliers to increase prices just to stay in the black. Plus, the same amount of demand for less readily available supply allows suppliers to drive up prices. Energy costs and policies around energy consumption are increasing transportation costs, contributing to higher price points.
Product complexity is also an issue for manufacturers. As the pace of innovation continues to accelerate, customers are demanding more features and functions for their products. Manufacturers need to be ready to quickly bring in new suppliers to meet time-to-market goals for new product introductions (NPIs). The need to grow relationships with suppliers as customer needs and business strategies shift increases the complexity of global supplier networks. Visibility into supplier quality is important for manufacturers looking to cut costs and improve product quality.
Best-in-Class Strategies for Addressing Supply Chain Pressures
So, the question becomes: what can manufacturers do to overcome these supply chain challenges and effectively predict scheduling, cost, and quality for raw materials? Looking at how Best-in-Class companies are handling supply chain quality reveals viable solutions.
Aberdeen defines Best-in-Class manufacturers as the top 20% of businesses based on their self-reported performance in key quality metrics, including the % of products meeting quality targets, % of products shipped with zero defects, cost of non-quality (recalls, warranty, etc.), and customer satisfaction. These top-performing organizations are more likely to track and leverage quality data to support supplier quality management.
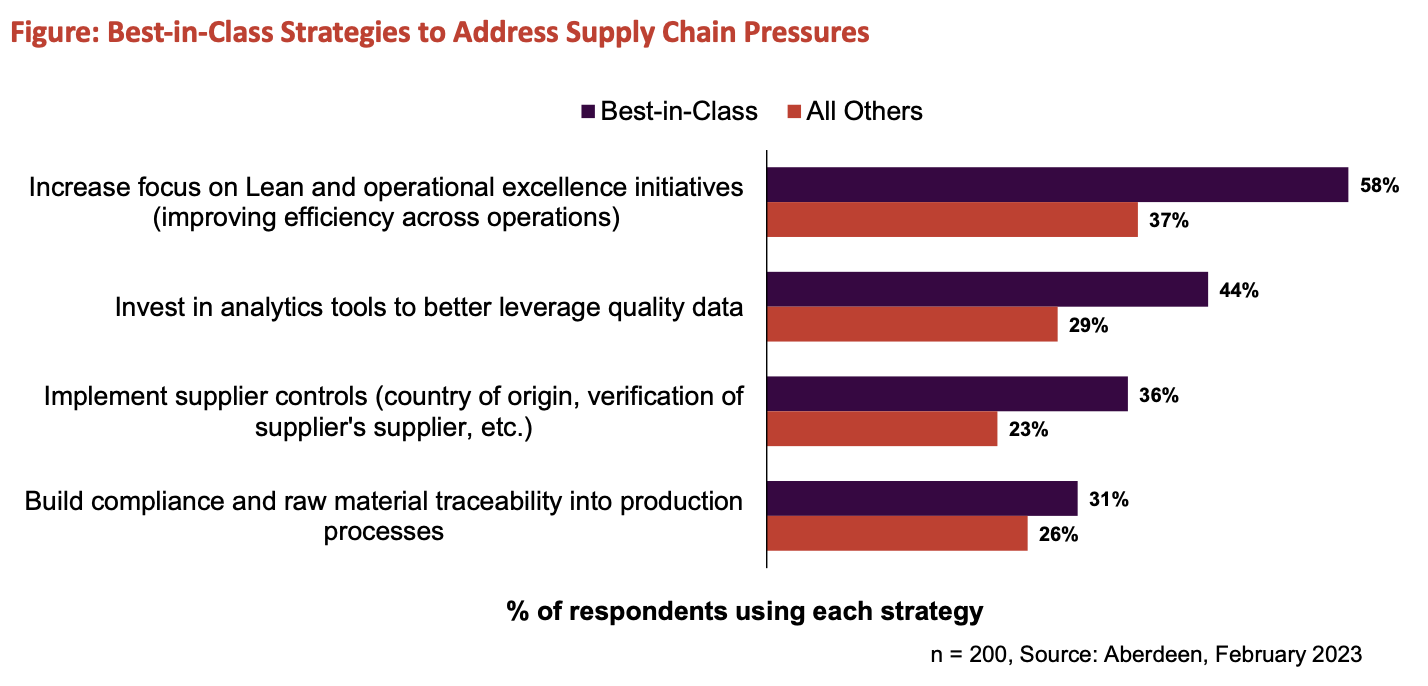
Figure: Best-in-Class Strategies to Address Supply Chain Pressures
1. Focus on Lean Manufacturing
Best-in-Class companies are more likely to focus on Lean manufacturing initiatives to reduce the amount of raw materials in inventory to support production. This involves cutting down on physical prototypes, design changes and ECOs, the space, movement, and operations for available inventory, and material waste wherever possible. With end-to-end solutions like PLM to monitor and optimize raw material utilization and traceability, Best-in-Class companies can cut back on spending and operating costs.
2. Build Compliance and Traceability into the Production Processes
To enable Lean manufacturing strategies, the Best-in-Class build compliance and raw material traceability into production processes to effectively track and measure utilization. Executive visibility into these metrics through dashboards and centralized databases allows business leaders to compare performance against targets and adjust as needed to achieve their Lean manufacturing goals.
3. Invest in Analytics
Best-in-Class manufacturers also invest in analytics to tie material quality back to suppliers. This allows them to prioritize relationships with suppliers who have historically provided high quality materials and stop working with those who don’t. Visibility into supplier quality at the enterprise level allows different teams and site locations to align supplier decisions with those insights. Supplier controls help to ensure standardization of supplier decisions across the company.
Benefits of Best-in-Class Strategies
These capabilities help the Best-in-Class plan and execute even during times of economic uncertainty. On average, Best-in-Class companies experience…
- Greater raw material quality – 48% more material lots/shipments/batches accepted within tolerance.
- Best-in-Class Avg: 74%
- All Others Avg: 50%
- Better relationships with suppliers – 44% more certified suppliers (their data is trusted for inspection results).
- Best-in-Class Avg: 75%
- All Others Avg: 52%
- Faster time-to-market – 47% more complete and on-time outbound shipments.
- Best-in-Class Avg: 72%
- All Others Avg: 49%
*Benchmark your organization’s performance against the Best-in-Class numbers above to see what changes you need to make to achieve Best-in-Class performance.
Start Implementing These Strategies Today
To summarize the importance of supplier quality for manufacturers, consider the common phrase: “The whole is greater than the sum of its parts”, meaning the work done together is better quality than the aggregated work of individual elements. But the quality of the parts is essential to the quality of the whole. If one part doesn’t pull its weight, the entire group can fail. That’s why leaders at Best-in-Class companies bring the right materials into their factories at the right time.
Closed-loop material quality management processes, enabled by traceability and analytics, allow Best-in-Class manufacturers to relay the defect and performance ratings of shipments back to procurement teams to optimize supplier selection. They can then build relationships with suppliers that are the most reliable and cost effective, boosting their batch acceptance rates and percentage of certified suppliers. They also prioritize Lean manufacturing to reduce the volume of raw materials to support their production needs, resulting in greater reductions in waste and operating costs.
Implementing these strategies can ultimately help any manufacturer get high-quality products out the door quickly with minimal change orders and defects, which leads to fewer recalls and warranty claims. By reaching time-to-market goals and keeping customers satisfied, manufactures can set themselves up for continuous operational efficiency, prospering with less time spent worrying about their supply chain and more time taking advantage of opportunities for innovation.